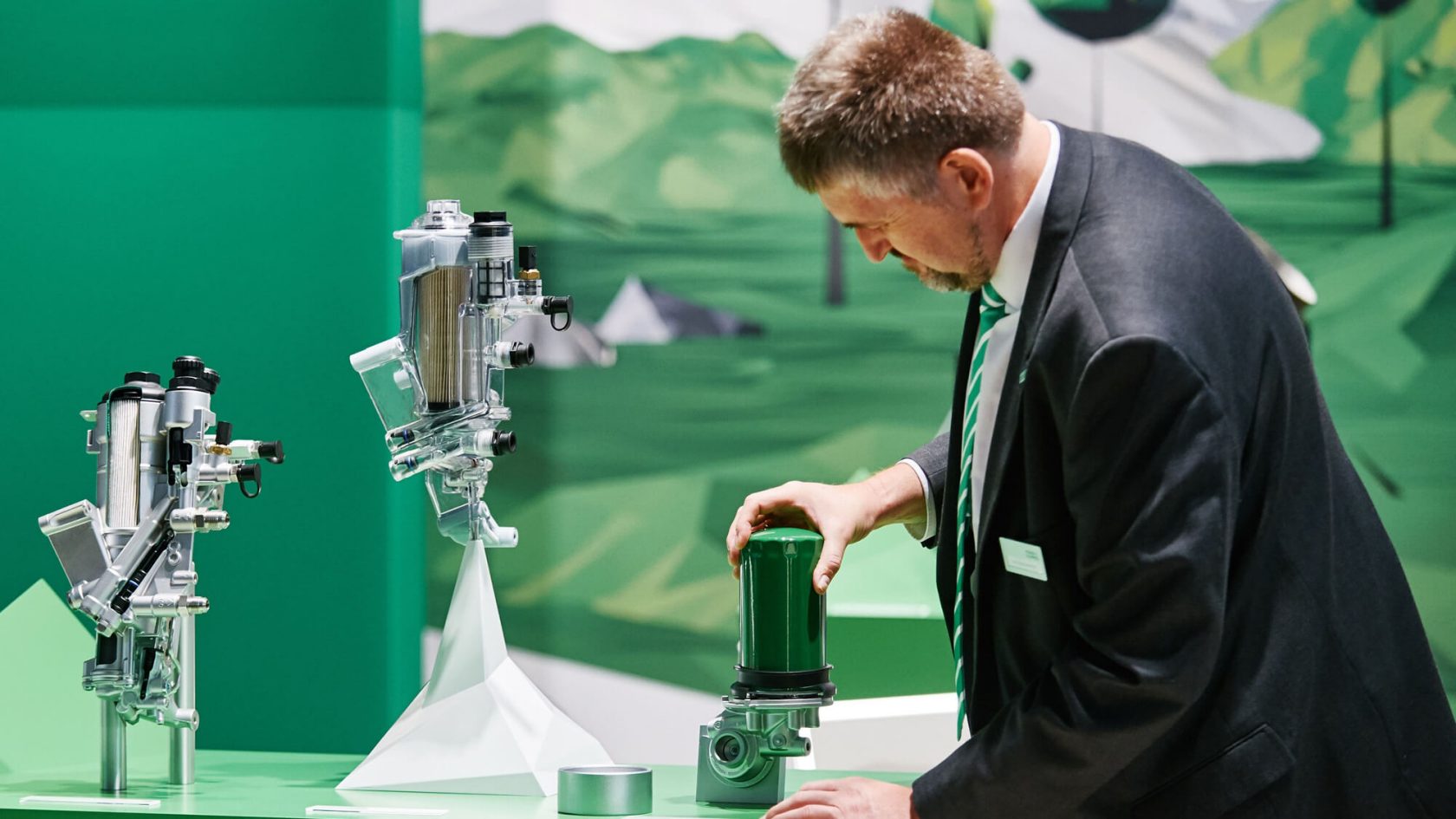
Perfect connection
Experts involved in the development of basic concepts, processes and series projects at MANN+HUMMEL have successfully developed and tested an innovative plastic-aluminum hybrid design for liquid filter modules used in trucks.

Plastic has proven itself over many years as a versatile material suitable for use in a wide range of applications in commercial vehicles and motor cars. There are limits, however, to the application of plastic in areas where components are subject to high thermal or mechanical stress since the relevant plastics can only achieve a certain strength and rigidity. Whereas MANN+HUMMEL introduced the world‘s first plastic oil filter module for cars in 2003, for reasons of stability filter modules in aluminum continue to be used in commercial vehicles. The specialists at MANN+HUMMEL looked for an alternative and developed a solution which also has the robustness required for these applications.

Best of both worlds
The aim of the developers was to combine the mechanical strength of aluminum with the design flexibility of plastic. The solution is an aluminum framework which is enclosed by a plastic envelope. In component areas where there is a high stress load such as flange joints or cover threads the metal absorbs and distributes the high local mechanical forces. This enables the component to withstand the respective load at these points. The housing envelope in plastic allows the easy integration of functions.
Complex design
The design of the component with this hybrid concept turned out to be complex. The aluminum framework, the so-called insert, has to absorb any forces which arise and transfer these through the interlocking of the plastic and aluminum. In this process stress peaks are to be avoided which could lead to a damage of the material. At the same time the insert has to be designed for the subsequent overmolding process and has to be able to be reliably fixed in the injection molding tool so that the overmolding process does not result in any deformation. Preliminary tests showed that given the different thermal expansion coefficients of the materials it is not possible to achieve a permanently sealed connection between the aluminum and plastic. In the contact area a tight connection between the aluminum and plastic cannot be ensured permanently. Therefore the developers designed all of the areas with contact to the media in plastic.
The polyamide used for the plastic envelope has a number of advantages with regard to flexibility. Although a die-cast process with multi-part tools can be used to achieve complex geometries, the production of a functional liquid filter module requires the subsequent machining of threads, sealing surfaces and hydraulic connections. This involves additional machining processes and high costs to be able to ensure the required degree of component cleanliness. The injection molding of a plastic part on the other hand enables the creation of all of the required connections and threads directly in the mold.
Costs which pay off

The new concept was validated through direct comparison with a fuel filter module for a 13.0 liter commercial vehicle engine. For this purpose samples in aluminum and also in the new plastic-aluminum hybrid design were tested on the test bench. The results were impressive. In particular in tests seen as very critical such as with high temperatures and alternating pressure loads or burst pressure strength the hybrid component achieved the same or better values than the aluminum housing.
The plastic-aluminum hybrid design can be seen as a real alternative to conventional aluminum solutions. In order to achieve a cost advantage, a number of conditions have to be met, for example, with regard to volume, design suitability for plastic and the necessity for machining. The additional tool required for the insert leads to higher costs. With higher volumes these costs are better distributed and as a result the hybrid concept can be described as economic. In addition, the maintenance of component cleanliness with aluminum housings is more cost intensive than with the hybrid module. If the insert and plastic remain unprocessed, this enables a reduction in costs.
The long-standing experience in the design of complex, highlystressed plastic components over many years and expertise in the conception of injection molding tools enables the specialists at MANN+HUMMEL to draw up a robust hybrid component which is able to meet the high requirements for commercial vehicles and is also economic. The first definite projects are currently being developed.